Parts washers catalog LINEA TUNNEL
Linear multistage parts washer for continuous treatment
Special system designed for high productivity and flexibility.
Usually used in productions where the quantity of pieces to be treated is very high and speed is a fundamental parameter.
These plants are composed of several consecutive phases where the pieces pass through thanks to a motorised transport system.
PHASES CONFIGURATION
These systems, by nature highly customised according to the customer's needs, can be configured in the project phase with the following stages:
• Load pieces
• Vapours aspiration
• Spray washing
• Spray rinses with demineralised water
• Spray rinses with antioxidant protection
• Compressed air blowing
• Hot air drying oven
• Parts cooling with compressed air
• Unloading pieces
LOADING AND UNLOADING OF PARTS
During the configuration phase it is possible to define different ways of loading and unloading pieces in line, among which:
Loading Modes
• Manual by operator
• Automatic from conveyor belt or customer's slide
• Automatic by customer's manipulator/robot
Discharge Modes
• Operator's manual
• Slide
• Automatic on conveyor belt or customer's slide
• Automatic by customer's manipulator/robot
TYPE OF HANDLING
Depending on the type and shape of the workpieces to be treated and the loading and unloading method, it is possible to configure the workpiece feed in different ways:
• On a stainless steel stainless steel flat conveyor belt in corrugated mesh
• On inclined stainless steel conveyor belt in corrugated mesh
• On conveyor belt with cross separators (e.g. for washing pipes and profiles)
• On simple stainless steel chains or with dedicated supports
• On dedicated pallets, designed specifically on the shape of the workpiece
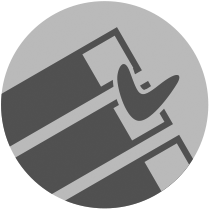
- HT (heating up to 80° C)
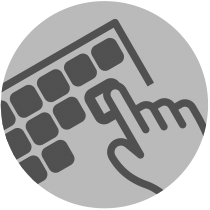
- PLC with color Touch Screen
- Industry 4.0 option
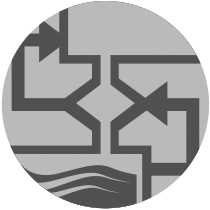
- Unique tank
- Double tank
- Triple tank
Video
Tunnel parts washers are the best option for a linear parts washing.
Parts are generally placed by operators on a conveyor belt going through all treatment phases up to the machine exit.
Tunnel parts washers are always designed and manufactured according to the process data: parts dimension and shape, hourly productivity, washing process type: degreasing, phosphating, rinsing, rust prevention, drying, cooling, etc.. Parts can be sometimes handled by a conveyor belt by means of two chains where supports are installed that are realized on the basis of the parts shape.
Steam extraction is ideal to evacuate steams generated during the washing phase.
Specific pipes covering the whole process area deliver washing and rinsing over the parts throughout.
Pressure is adjustable by appropriate lockable valves whereas internal pipes are installed on quick fastening fittings, thus ensuring an easy maintenance.
Hot-air drying is performed by electric blowers that take in the filtered air from exterior and spray it out through blade-nozzle pipes heated by electric resistors.
Parts loading: manual, by anthropomorphic robot, with slide falling modes.
Parts unloading: manual, by anthropomorphic robot (with or without vision system), with slide falling modes.
Tunnel parts washers can be customised according to the parts type (e.g.: for metal pipes or profiles washing the belt is sloping down for the detergent liquid dripping) or the customer's layout (e.g.: parts unloading on the returning belt or conveyor with pick & place system, oval shaped conveyor or chain belt for handling the parts loading and unloading from a single site).
In-line washing of electric capacitors
Find out how Teknox solved the challenge of in-line washing of electric capacitors contaminated with toxic substances.